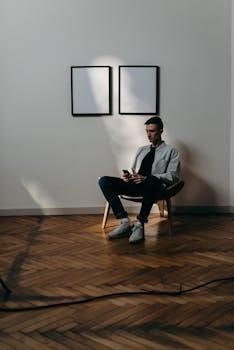
carbon fiber frame joint connection design pdf
Carbon Fiber Frame Joint Connection Design⁚ A Comprehensive Overview
This overview delves into the complexities of carbon fiber frame joint design, encompassing adhesive bonding, mechanical joints, and stress distribution. It explores maximizing performance with joint design and adhesive selection, including the durability.
Carbon fiber reinforced polymer (CFRP) composites offer an alternative to conventional materials like steel or aluminum, enabling the construction of lightweight trusses and frame structures. The design considerations for carbon fiber frames differ significantly from those of traditional materials due to the anisotropic nature of CFRP and the importance of joint design in maintaining structural integrity. Carbon fiber’s high strength-to-weight ratio makes it ideal for applications where weight reduction is critical, such as in automotive, aerospace, and sporting goods industries. In Formula Student competitions and Formula 1 cars, CFRP monocoques have become widely used for cock-pits, replacing traditional steel frames. These monocoques, sandwich structures of carbon fiber skin and aluminum honeycomb, exemplify the advanced application of carbon fiber in frame design. Key to the success of carbon fiber frames is the robust design of their joints, as these areas are often prone to failure due to concentrated stresses in fillets and connections. Understanding the specific properties of carbon fiber and how it interacts with different jointing methods is crucial for creating durable and reliable structures. The selection of appropriate materials, the geometry of the joint, and the manufacturing process all play a vital role in the overall performance of the carbon fiber frame. Proper joint design is not only essential for structural integrity but also for the aesthetic appeal of the final product; Therefore, a comprehensive understanding of carbon fiber’s characteristics and the various jointing techniques is paramount for engineers working with these advanced composite materials.
Adhesive Bonding Technology in Carbon Fiber Joints
Adhesive bonding provides a strong, lightweight, and aesthetically pleasing solution for joining carbon fiber structures. The design of the adhesive joint is crucial, as its geometry significantly influences stress distribution and overall strength. Unlike mechanical joints, adhesive bonding distributes stress more evenly across the joint area, reducing stress concentrations. However, the durability of the joint depends heavily on selecting an adhesive with appropriate physical properties, particularly its ability to evenly distribute the load to the upper matrix of the composite. Engineers often design lab shear joints to evaluate adhesives, although these joints may not perfectly represent real-world structural conditions where both shear and peel stresses occur. The Ramp;D activities focus on adhesive bonding technology, surface technology, and fiber composite technology. The importance of choosing an Adhesive with appropriate physical properties for the design is great. Particularly for fiber-reinforced materials, the durability of the joint is determined by the capability of the adhesive to evenly distribute the load.Several researchers have found significant performance Maximizing Performance with Joint Design and Adhesive Selection. Bonded structures are exposed to a combination of different loadings, including tensile, compressive, shear, cleavage, and peel stresses. Surface preparation of the carbon fiber is also critical for achieving a strong and durable bond. Factors to consider include cleaning the surface to remove contaminants, applying a primer to enhance adhesion, and controlling the bonding environment to ensure proper curing of the adhesive. The long-term performance of adhesive bonds can be affected by environmental factors such as temperature, humidity, and exposure to chemicals, necessitating careful consideration of these factors during adhesive selection and joint design.
Mechanical Joint Design⁚ Bolts and Rivets in CFRP Connections
Mechanical joints, utilizing bolts and rivets, represent another approach to joining carbon fiber reinforced polymer (CFRP) components. While adhesive bonding offers advantages in stress distribution, mechanical joints provide a readily inspectable and potentially disassemblable connection method. However, the introduction of holes for fasteners can disrupt the continuous fiber structure of the CFRP, leading to stress concentrations around the hole edges and potentially reducing the overall strength of the component. High Modulus (HM) carbon fiber reinforced polymer strips are a pultruded laminate with sufficient strength and stiffness to strengthen steel structures, as shown in Figure 1. The carbon fiber’s performance is maximised through joint design. Joint Design⁚ Stack-up, material gage, rivet material type Design allowances for manufacturing implementation Joint Performance Ultrasonic Welding Manufacturing implementation⁚ Flexible tooling Process development⁚ Specificity -Welding schedules -Process/quality monitoring Joint performance /servo (1) Pressure amp; high frequency. The reference scope for the FLCM is a complex structure of multiple steel and plastic components joint with bolts and rivets. The FLCM structure. When a metal and carbon fibres are bonded together, there is a risk for corrosion on the metal due to different electronic potential in the materials. Design considerations for bolted and riveted CFRP joints include selecting appropriate fastener materials to avoid galvanic corrosion with the carbon fiber, optimizing hole spacing and edge distances to minimize stress concentrations, and using torque control during fastener installation to prevent over-tightening and potential damage to the composite material. In some joint designs, load sharing between the adhesive and the bolt is desired to improve joint strength and durability. Ultrasonic welding is also a method of joint performance.The FLCM is a complex structure of multiple steel and plastic components joint with bolts and rivets.
Stress Distribution and Joint Geometry Considerations
The geometry of a carbon fiber frame joint significantly influences stress distribution and, consequently, the overall strength and durability of the connection. Sharp corners and abrupt changes in cross-section can act as stress concentrators, leading to premature failure. Therefore, careful attention must be paid to designing smooth transitions and incorporating generous radii at joint interfaces. The design of the bonded joint itself is important; the geometry of the joint influences the stress distribution and overall strength. The design of the adhesive joint is governed by stresses that are critical near the ends of the HM strip. Several researchers have found significant performance in their designs. Engineers usu- ally design some form of lab shear joint for use with adhesives. These joints are not ideal structurally because under load both shear and peel. Areas that are prone to failure are located in the fillets and joints due to stress. When a metal and carbon fibres are bonded together, there is a risk for corrosion on the metal due to different electronic potential in the materials. In adhesive joints, the shape and overlap length play crucial roles in distributing stress evenly across the bonded area. Tapered or scarf joints, for example, can reduce peel stresses at the bond edges, improving the joint’s resistance to fatigue and environmental degradation. Similarly, in mechanically fastened joints, the spacing and arrangement of fasteners affect the load distribution among them. Optimizing fastener patterns can minimize stress concentrations around individual holes and enhance the joint’s overall load-carrying capacity. Finite element analysis (FEA) is a valuable tool for evaluating stress distributions in complex joint geometries and identifying potential weak points. By simulating various loading scenarios, engineers can refine their designs to achieve more uniform stress distributions and improve joint performance. The choice of joint configuration must also consider the specific loading conditions the frame will experience. Joints subjected to tensile loads may require different designs than those primarily loaded in shear or compression;
CFRP Monocoque Structures in Racing Applications
Carbon Fiber Reinforced Polymer (CFRP) monocoque structures have revolutionized racing car design, offering unparalleled strength-to-weight ratios and stiffness, crucial for maximizing performance on the track. In the Formula Student (FS) competition, carbon fiber reinforced polymer (CFRP) monocoque, which is the same as Formula 1 cars has been widely used in the cock-pit of racing cars to replace the traditional steel frame structure. As shown in Fig. 1, the CFRP monocoque is a sandwich structure composed of carbon fiber skin and aluminum. These single-shell structures provide a protective and structurally sound chassis, integrating the frame and body into a single unit. The adoption of CFRP monocoques stems from their ability to meet stringent safety requirements while minimizing weight, a critical factor in achieving optimal acceleration, braking, and handling. The design of a CFRP monocoque involves complex considerations of laminate layup, core materials, and joint configurations. The carbon fiber plies are strategically oriented to maximize stiffness in the directions of primary load paths, ensuring the structure can withstand the extreme forces generated during racing. Core materials, such as honeycomb or foam, provide support to the thin carbon fiber skins, preventing buckling and increasing overall structural integrity. Joint design is paramount in CFRP monocoques, as these connections must transfer loads efficiently between different sections of the structure. Adhesive bonding is commonly employed to join CFRP components, creating strong and lightweight connections. Mechanical fasteners, such as bolts or rivets, may also be used in conjunction with adhesives to provide additional security and redundancy. The design of these joints must account for stress concentrations and potential failure modes, ensuring the monocoque can withstand the rigors of racing. The monocoque is a sandwich structure composed of carbon fiber skin and aluminum. The benefits were only observed in joint designs which allowed for load sharing between the adhesive and the bolt.
Reinforcement of Beam-Column Joints with CFRP Rods
Reinforcing beam-column joints with Carbon Fiber Reinforced Polymer (CFRP) rods offers a compelling solution for enhancing the structural integrity and load-bearing capacity of these critical connections, particularly in applications where weight reduction and increased strength are paramount. This technique involves embedding CFRP rods within the joint region, effectively increasing the joint’s resistance to shear and flexural forces. This study proposed a new design to reinforce the beam-column joints with embedded carbon fiber-reinforced polymer (CFRP) rods, due to their extremely high strength. The high tensile strength and stiffness of CFRP rods make them ideal for reinforcing concrete or composite beam-column joints, improving their ability to withstand seismic loads, impact forces, and other extreme conditions. The design process for CFRP rod reinforcement involves careful consideration of several factors, including the size and spacing of the rods, the embedment depth, and the adhesive used to bond the rods to the surrounding material. Finite element analysis (FEA) is often employed to optimize the reinforcement configuration and predict the stress distribution within the joint. The use of CFRP rods can significantly improve the performance of beam-column joints in several ways. First, the rods increase the joint’s shear capacity, preventing shear failure under high loads. Second, they enhance the joint’s flexural capacity, allowing it to resist bending moments more effectively. Third, the CFRP rods improve the ductility of the joint, increasing its ability to deform without fracturing. This is particularly important in seismic applications, where joints must be able to withstand large deformations without collapsing. The effectiveness of CFRP rod reinforcement has been demonstrated in numerous experimental studies and field applications. These studies have shown that CFRP rods can significantly increase the strength and ductility of beam-column joints, improving the overall safety and reliability of structures. The use of CFRP rods is a cost-effective and efficient way to upgrade existing structures or to design new structures with enhanced performance characteristics. The study proposed a new design to reinforce the beam-column joints with embedded carbon fiber-reinforced polymer (CFRP) rods, due to their.
Failure Modes in Carbon Fiber Composite Joints
Understanding the failure modes in carbon fiber composite joints is crucial for designing reliable and durable structures. These joints, whether adhesively bonded or mechanically fastened, are often the weakest points in a composite structure and are susceptible to various failure mechanisms under different loading conditions. Identifying and mitigating these failure modes is essential for ensuring the structural integrity and longevity of carbon fiber composite components. One common failure mode in adhesively bonded joints is adhesive failure, which occurs when the adhesive bond between the carbon fiber composite and the adherend fails. This can be caused by insufficient surface preparation, improper adhesive selection, environmental degradation, or excessive stress concentrations. Cohesive failure, on the other hand, occurs within the adhesive layer itself, indicating that the adhesive’s internal strength has been exceeded. Another significant failure mode is interlaminar failure, also known as delamination, which involves the separation of the carbon fiber composite plies. This can be triggered by peel stresses, interlaminar shear stresses, or impact damage. In mechanically fastened joints, failure can occur through bearing failure, where the fastener crushes the composite material around the hole, or through shear-out failure, where the composite material shears off between the hole and the edge of the component. Tensile failure of the composite material can also occur if the joint is subjected to excessive tensile loads. The geometry of the joint plays a crucial role in determining the stress distribution and the likelihood of failure. Sharp corners and abrupt changes in cross-section can create stress concentrations that can initiate failure. Therefore, careful attention must be paid to the joint design to minimize stress concentrations and ensure a more uniform stress distribution. Environmental factors, such as temperature and humidity, can also significantly affect the performance of carbon fiber composite joints. Elevated temperatures can weaken the adhesive bond and reduce the strength of the composite material, while humidity can lead to moisture absorption, which can degrade the adhesive and the composite matrix. The study of failure modes of carbon fiber composite joints is of great significance for the reasonable design of aircraft structural details. Many scholars have done much research on the connection structure of carbon fiber composite materials in recent years. Zeng et al. 8 studied the failure prediction of com-posite sandwich L-shaped joints under bending.
Durability and Adhesive Selection for Carbon Fiber Joints
Aluminum Inserts for Enhanced Connection in Carbon Fiber Parts
Aluminum inserts are frequently employed in carbon fiber composite structures to enhance connection strength and provide reliable interfaces for mechanical fastening. The integration of aluminum inserts addresses several challenges associated with directly joining or fastening to carbon fiber composites, such as their susceptibility to crushing under compressive loads and their limited ability to distribute stress effectively around fastening points. By incorporating aluminum inserts, engineers can leverage the high strength-to-weight ratio of carbon fiber while ensuring robust and durable connections. The general approach includes aluminum inserts in the carbon fiber part. These inserts offer good connection and bolting surfaces as well as a nice load transfer mechanism. Aluminum, with its superior compressive strength and ductility compared to carbon fiber composites, can withstand higher clamping forces and distribute load more evenly, preventing damage to the composite material. Aluminum inserts are typically integrated into the carbon fiber part during the manufacturing process, often through co-curing or adhesive bonding. Co-curing involves placing the aluminum insert within the carbon fiber layup before the composite is cured, allowing the resin to bond directly to the aluminum surface. This creates a strong and durable connection between the insert and the composite material. Adhesive bonding is another common method for attaching aluminum inserts to carbon fiber parts. A structural adhesive is used to bond the insert to the composite surface, providing a high-strength and reliable connection. The selection of the appropriate adhesive is crucial to ensure compatibility with both the aluminum and carbon fiber materials and to withstand the anticipated loading conditions and environmental factors. The design of the aluminum insert is also critical to its performance. Inserts are often designed with features such as flanges, threads, or knurled surfaces to enhance bonding and provide secure attachment points. The geometry of the insert should be optimized to minimize stress concentrations in the carbon fiber composite and to ensure a smooth load transfer between the insert and the composite material. In addition to enhancing mechanical fastening, aluminum inserts can also provide other benefits, such as improved thermal conductivity and electrical conductivity. Aluminum is a good conductor of heat and electricity, so incorporating aluminum inserts can help to dissipate heat and provide grounding points in carbon fiber composite structures. However, when a metal and carbon fibres are bonded together, there is a risk for corrosion on the metal due to different electronic potential in the materials. The metal…